Air Tindi operates a fleet of DHC-7 (Dash 7) aircraft primarily in Canada’s north. Operating this close to the Earth’s magnetic poles presents an interesting problem for modern magnetometer systems. Together Air Tindi, Maxcraft, and our vendors developed a solution to modernize this fleet with a glass panel avionics solution which is optimized for northern operations.
Dash 7 Glass Flight Deck Optimized for the North
De Havilland DHC 7 (Dash 7)

Aircraft & Owner:
The Dash 7 is yet another classic Canadian aircraft. Developed by de Havilland Canada (The same aircraft manufacturer that brought us the world-renowned DHC-2 Beaver, DHC-3 Turbo Otter, and DHC-6 Twin Otter) in the 1970s to compete with larger regional airliners, while still maintaining the Short Take-Off and Landing (STOL) characteristics de Havilland is known for. This resulted in a nearly one-of-a-kind aircraft which is still hard to beat by options on the market today, and has become irreplaceable to operators like Air Tindi who operate in remote regions, often fully utilizing the Dash 7’s STOL, and off airport capabilities.
Air Tindi is Northern Canada’s leading air charter and scheduled service provider. Canada’s North is home to some of the most remote communities on Earth. With some of these places only being accessible by aircraft, Air Tindi provides a vital link to community members with air cargo services, daily scheduled flights, Air Ambulance services, and charter flights. With a diverse fleet of over 25 aircraft, Air Tindi can fly anywhere in North America from their base in Yellowknife, NWT. Even in places where the nearest airport is hundreds of kilometers away, Air Tindi can get there thanks to their highly skilled crews, and aircraft on skis, floats, and tundra tires.
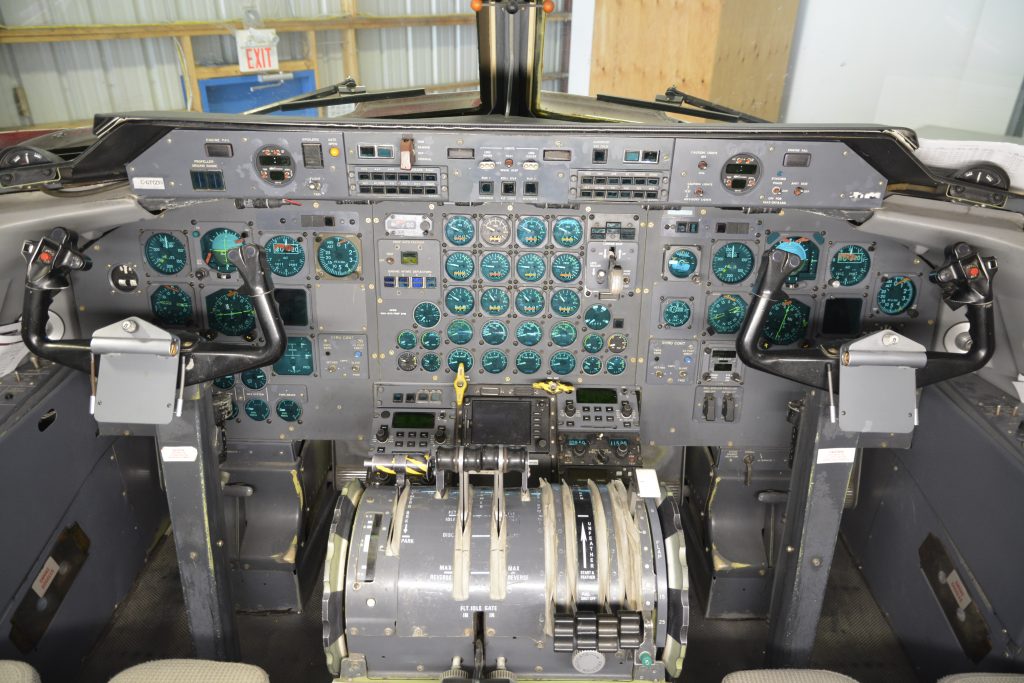
Need:
Air Tindi currently has the largest fleet of Dash 7 aircraft still flying today. While the Dash 7 fits their mission profile perfectly, the avionics were showing their age and becoming less and less reliable which can result in large costs, whether in the form of downtime or repair bills. Over the past few years, Maxcraft has been working closely with the team at Air Tindi to understand their operations, their pain points, and to find the ideal solution which would support the harsh environment their aircraft are often flying in and out of.
One of the primary struggles Air Tindi faced when exploring upgrade paths for this airframe was the unreliability of compass systems (including magnetometers) in locations close to the Earth’s magnetic poles. While many pilots may only vaguely remember learning about compass errors at extreme north or south latitudes during their ground school, this is an everyday reality for Air Tindi’s flight crews. This environment really calls for a high precision Attitude Heading and Reference System (AHRS), along with a way to ignore the on-board magnetometer when operating in areas of magnetic unreliability.
By working closely with our equipment manufacturers, our in-house Design Approval Organization (DAO), Transport Canada, and of course Air Tindi, Maxcraft was able to develop a solution based around Garmin’s G700 TXi Primary Flight Display (PFD) system and high precision GRS 7800 AHRS with a custom software feature called “Free Gyro Mode” allowing pilots to engage in areas of compass unreliability. The system design and approval efforts were significant and required months of effort by our DAO team. The end result was the issuance of seven new STC approvals to cover the various system upgrades.
Simplifying one example use case of Free Gyro Mode: The pilot will enable Free Gyro Mode while on the ground (often while lined up on the runway, using the runway heading) setting the heading on their PFD, and disabling the automatic updates of the heading via the magnetometer. This will result in the heading on the primary flight display acting much like a traditional directional gyro in the sense that it follows the movements of the aircraft rather than picking up on the Earth’s magnetic field.
Being a Transport Category aircraft (Equivalent of FAR Part 25 in the United States), a project of this magnitude is a significant undertaking by all parties involved and required working directly with Transport Canada to satisfy their requirements. This also meant we would be working to a higher level of redundancy. As a multi-crew aircraft, you’ll find both pilot seats are equipped with the same avionics.
NEW EQUIPMENT LIST
G700 TXi x2 | Dual 10.6” Integrated Primary Flight Display with SVT (Garmin) |
GI 275 x2 | Dual Standby Electronic Flight Instrument (Garmin) |
GTN 750 Xi x2 | Dual 6.9” Touchscreen Flight Navigator and Multifunction Display (Garmin) |
GCU 485 x2 | Dual Primary Flight Display Controller (Garmin) |
TAWS-A Enablement | Terrain Avoidance and Warning System (TAWS) on GTN 750 Xi (Garmin) |
GTS 8000 | TCAS II Traffic Collision Avoidance System (Garmin) |
GTX 3000 x2 | ADS-B Out Transponder with TCAD II/ACAS II Compatibility (Garmin) |
GWX 75 | Digital Doppler Enabled Weather Radar (Garmin) |
GWX 8000 | StormOptix Enablement for GWX 75 (Garmin) |
ALT-4000+ | 5G Resilient Radar Altimeter (Collins Aerospace) |
LSA100-100 | Cabin PA Amplifier (Anodyne Electronics Manufacturing) |
GDL 60 | Datalink with PlaneSync™ Technology (Garmin) |
GSR 56 | Satellite Datalink System (Garmin) |
GRS 7800 | Attitude and Heading Reference System (AHRS) with Free Gyro Mode (Garmin) |
GDC 7400 | Air Data Computer (Garmin) |
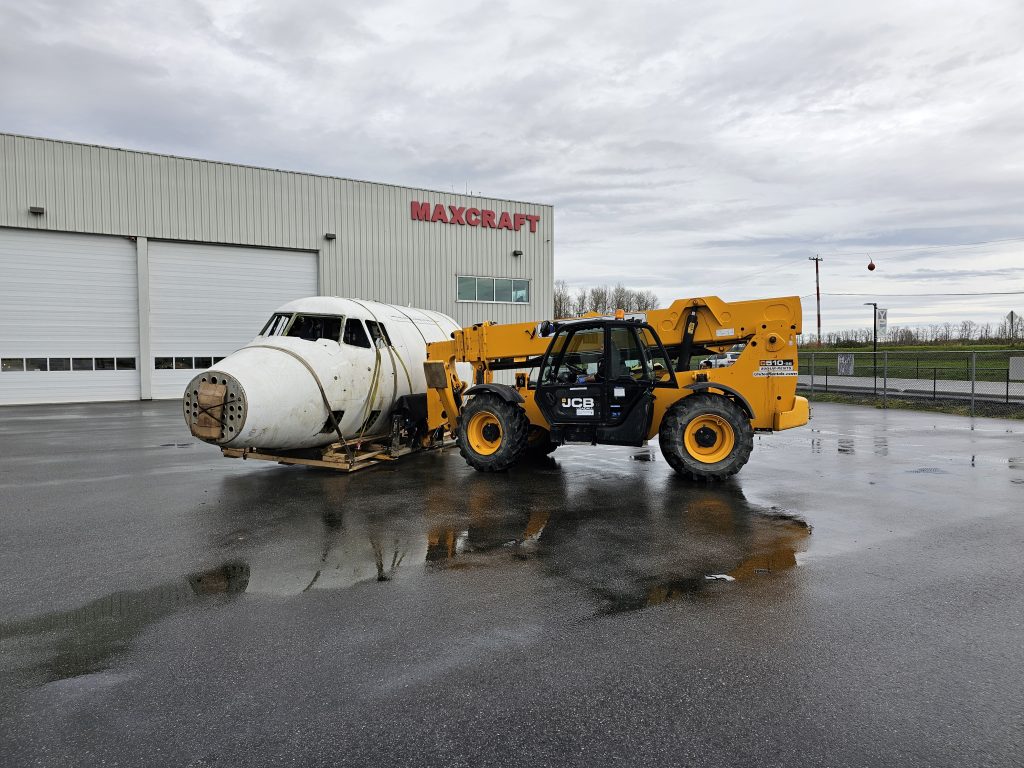
Maxcraft Solution:
Once we knew the direction we wanted to go with this project, and a buy-in from all the relevant parties, the fun began. Before even finalizing the quote, Air Tindi presented us with an interesting proposal…
They had a scrap Dash 7 sitting at their base in Yellowknife and asked us if the flight deck portion of the fuselage would be of use to us. Having this section of the aircraft would be invaluable to us, allowing us to complete much of the design portion of the project, such as fabricating mounting hardware, determining wirelengths to create wiring harnesses ahead of time, and even some antenna locations, this tool would allow us to significantly reduce the downtime of an in-service aircraft, and ultimately reduce Air Tindi’s lost revenue at the same time. Shortly after our agreement to this proposal Air Tindi’s crew got to work sawing this iconic aircraft into a ¼ section, lifting it onto a truck, and sending it on the long voyage from Yellowknife, to ultimately arrive at Maxcraft in Pitt Meadows.
After some work by our design group and avionics technicians on the shell fuselage, software development by Garmin, coordination with Air Tindi and many others around the Pitt Meadows Airport to accommodate an aircraft of this size, we were ready for the first aircraft in the fleet.
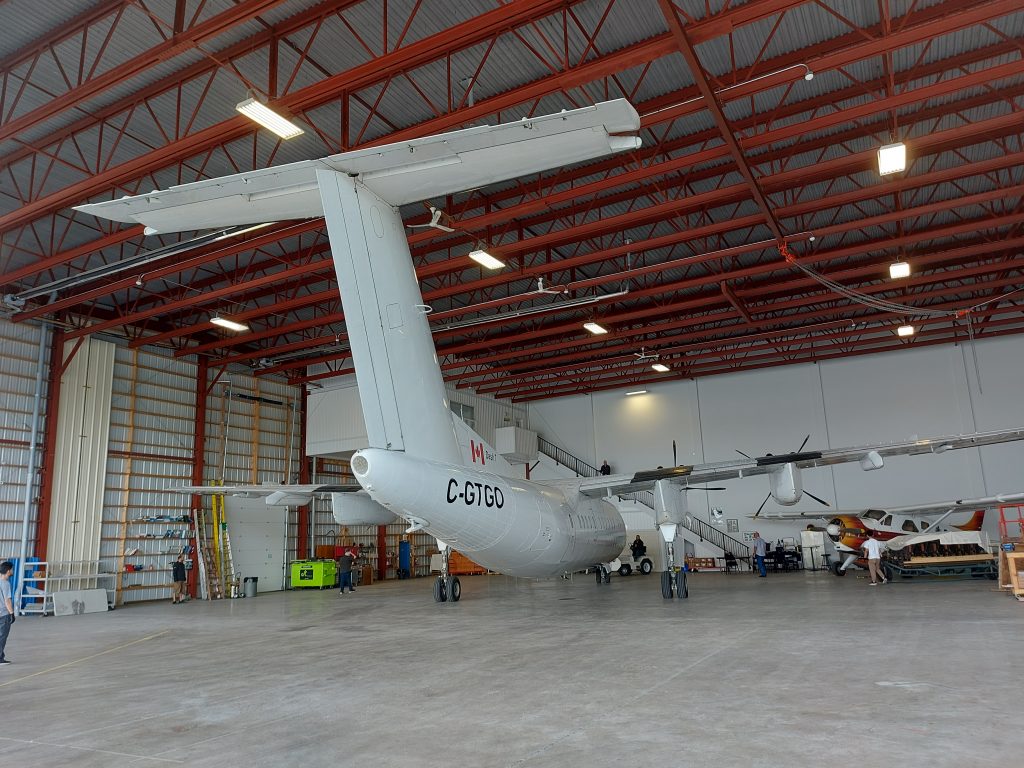
The Story:
After the aircraft arrived, both Maxcraft and Air Tindi were quick to get to work, tearing the aircraft apart. Concurrent to our avionics upgrade project, Air Tindi also used the downtime of this aircraft to complete a “C” phase check, which is a mandatory comprehensive inspection of the aircraft. With this being our first time working on the Dash 7 airframe, we were often emailing, calling, or asking Air Tindi staff onsite niche questions about the airframe. As the largest operator of the Dash 7, Air Tindi’s maintenance staff have become experts and know the airframe inside and out, and their pointers and shared wisdom undoubtedly saved us significant time on this project.
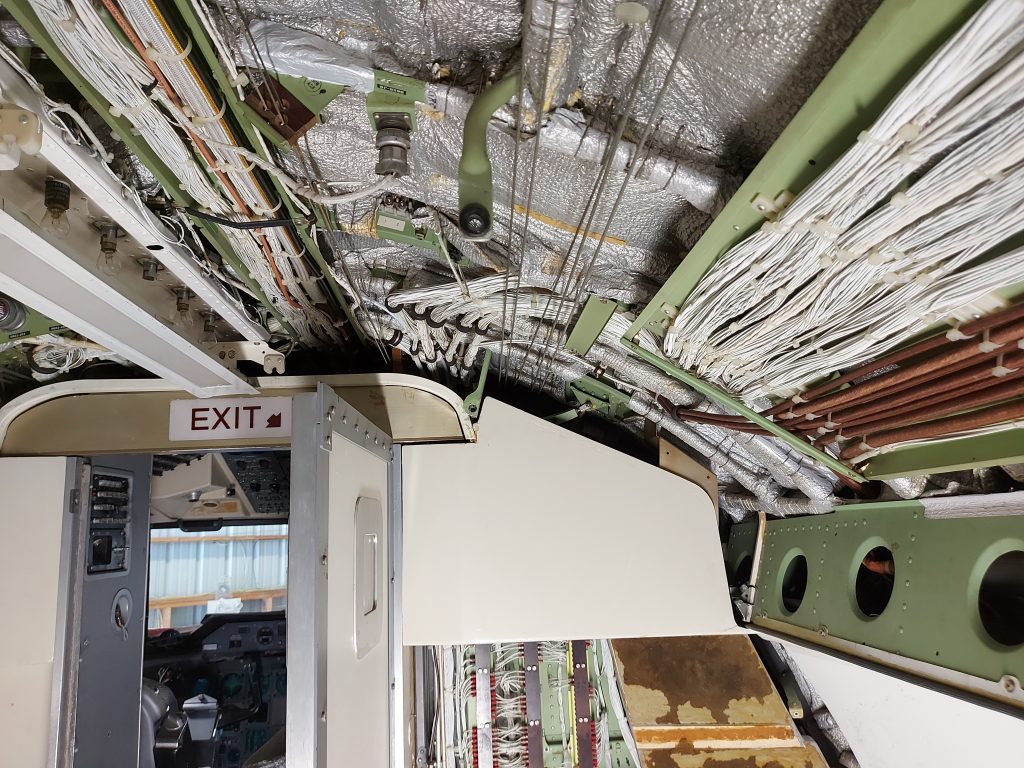
The Dash 7 is definitely one of the more complex airframes we’ve worked on, but we were up to the task. After removing most of the old avionics, our team began installing new mounting structure, routing new wiring harnesses, and testing how the new equipment interfaced with the retained equipment.
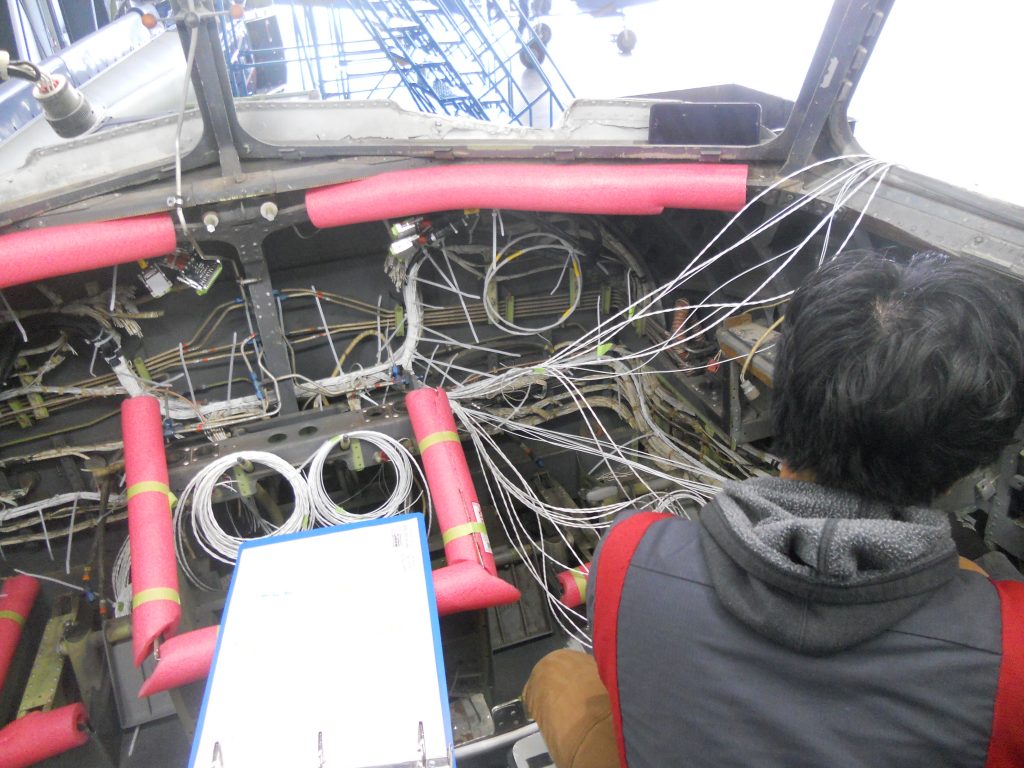
One of the most challenging aspects of this project was integrating the modern digital avionics to the older systems in the Dash 7, most of which were original to the 1970s. This upgrade would retain the original autopilot system, and dual flight directors, which was one of our pinch points in terms of integration. We also had to integrate a modern audio panel system with the original flight attendant call station to ensure the pilots can communicate with the cabin crew during all phases of flight.
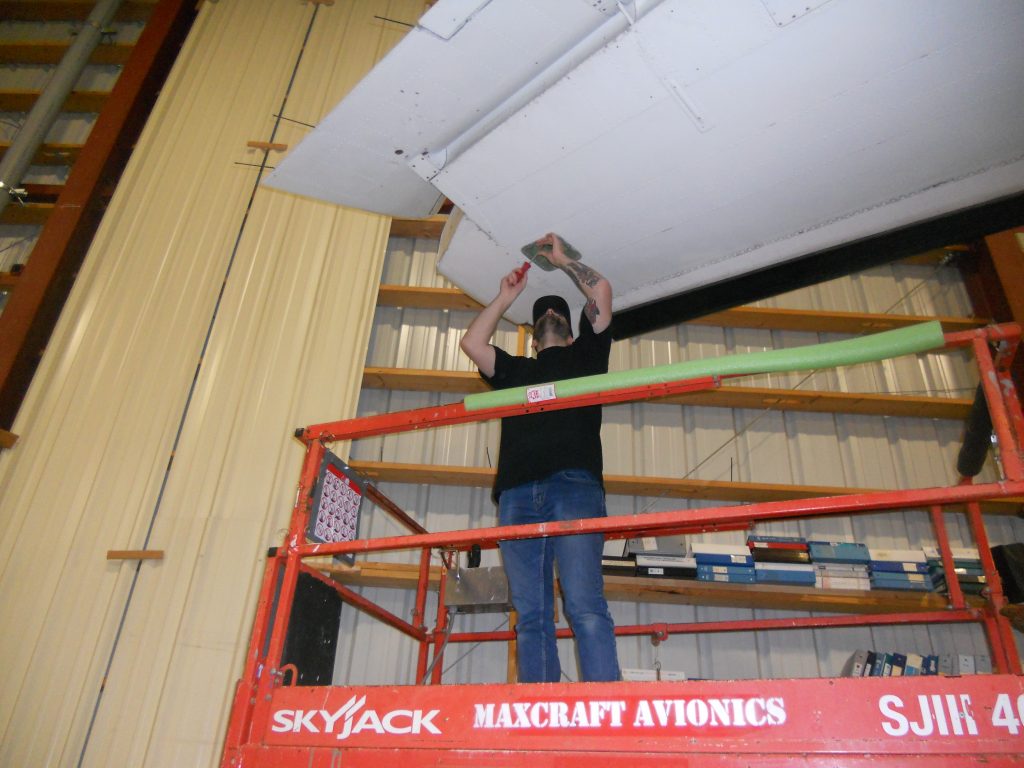
Garmin’s GDL 60 is a recent addition to Garmin’s lineup, but Air Tindi was eager to include it in this project. Garmin’s PlaneSync technology is a game changer for aircraft owners, and a must have for fleet operators. The GDL 60 uses a combination of LTE cellular, and Wi-Fi connectivity to keep all the databases on the avionics stack up to date, greatly reducing the time traditionally spent by maintenance crew manually updating them every cycle using SD cards. PlaneSync will also push flight logs from the avionics to the cloud automatically at the end of a flight. This data can be used by maintenance and flight ops crew to review any abnormal occurrences reported by the flight crew to possibly determine the cause.
Operating in some of the most remote and inhospitable locations in Canada, connectivity is a must throughout the entirety of the flight. Garmin’s GSR 56 provides a satellite link to the world no matter how remote of a location the aircraft is in. The GSR 56 adds satellite tracking, and two-way messaging, allowing flight operations personnel to communicate with the pilots, and track the exact location of the aircraft, even when they are on the ground at a remote, off-airport landing strip. Additionally, the GSR56 provides up to date weather information to the pilots, allowing them to strategically plan routing, and arrival procedures.
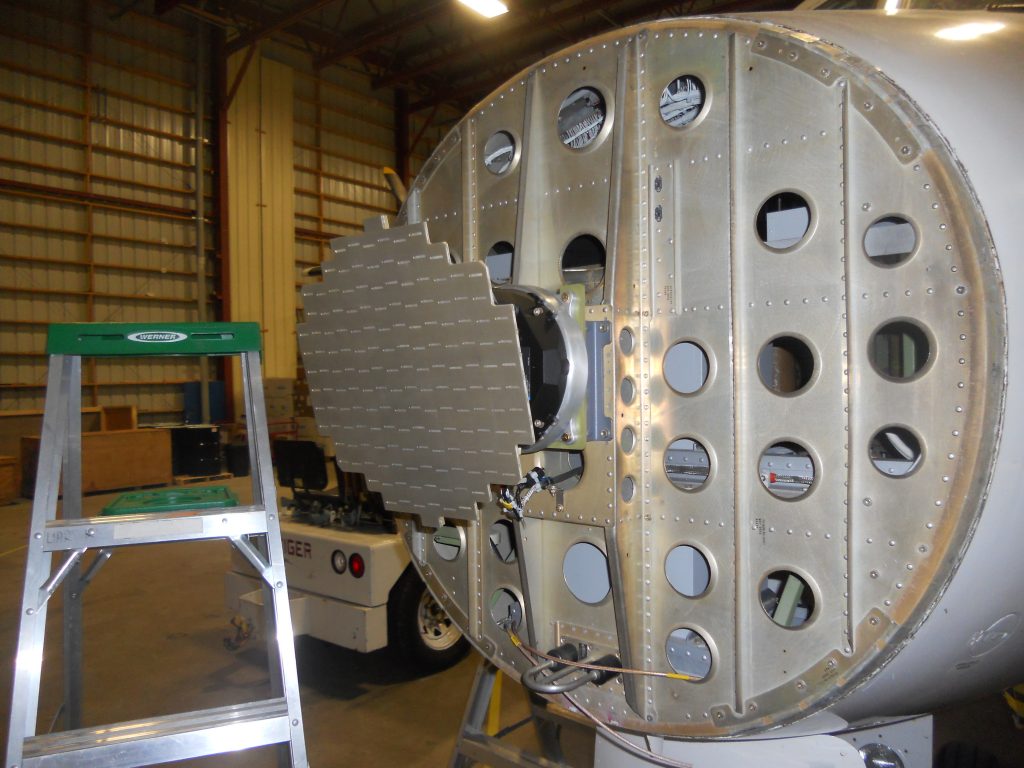
Canada’s North can also be home to some of the most extreme weather conditions found anywhere. With minimal traffic to provide PIREPS, pilots often need to “find their own way” through storms. A weather radar allows pilots to make real time navigation decisions to avoid the worst of the weather by providing them with a full picture of what’s going on ahead of them. Garmin’s GWX 75 digital weather radar is one of the best solutions on the market, and when combined with their GWX 8000 StormOptix technology, this system will display more storm detail, while also simplifying operation through features such as Auto Mode, and enhancing situational awareness.
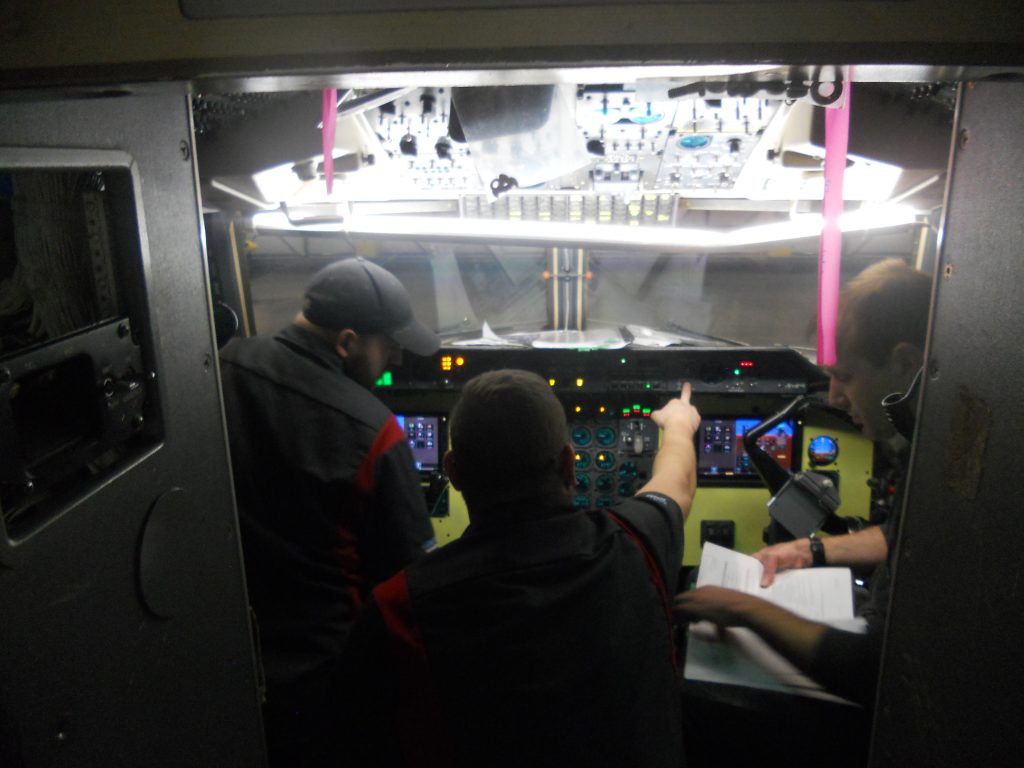
After the equipment was finally installed, we were required to complete countless ground test procedures, both inside the hangar, and out on the ramp with all the engines running to ensure there weren’t any electromagnetic interference or vibration issues. While the completion of tests like these will often feel like the end of a project, this time was much different. Once all the equipment was installed, configured, integrated, and ground tested, we had to begin coordinating with Air Tindi, Transport Canada, and our partners around Pitt Meadows airport to arrange flight testing windows.
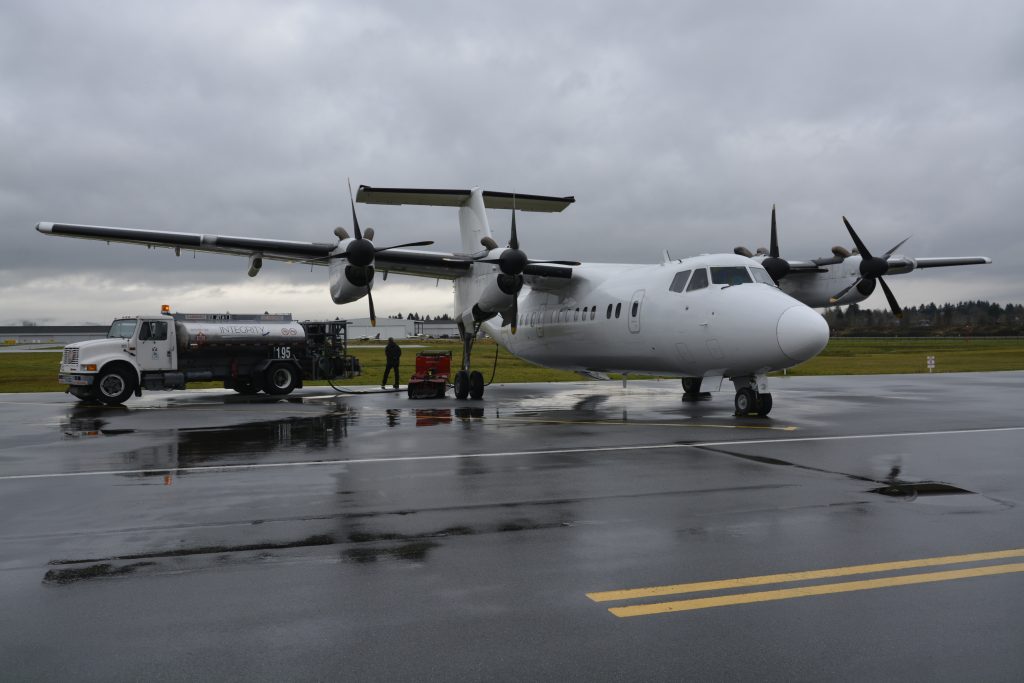
While test flights after installations are often just a chance to run through some simple tests of the new avionics, maybe completing a few maneuvers, approaches to make sure everything works as expected, a project of this size on an aircraft in the Transport Category requires a whole other level of attention to detail. With a flight test permit issued by Transport Canada, the new age of the Dash 7 took flight and was fully put through a number of situations to test many conditions which may be expected in real world flying to ensure the avionics continue to operate as intended.
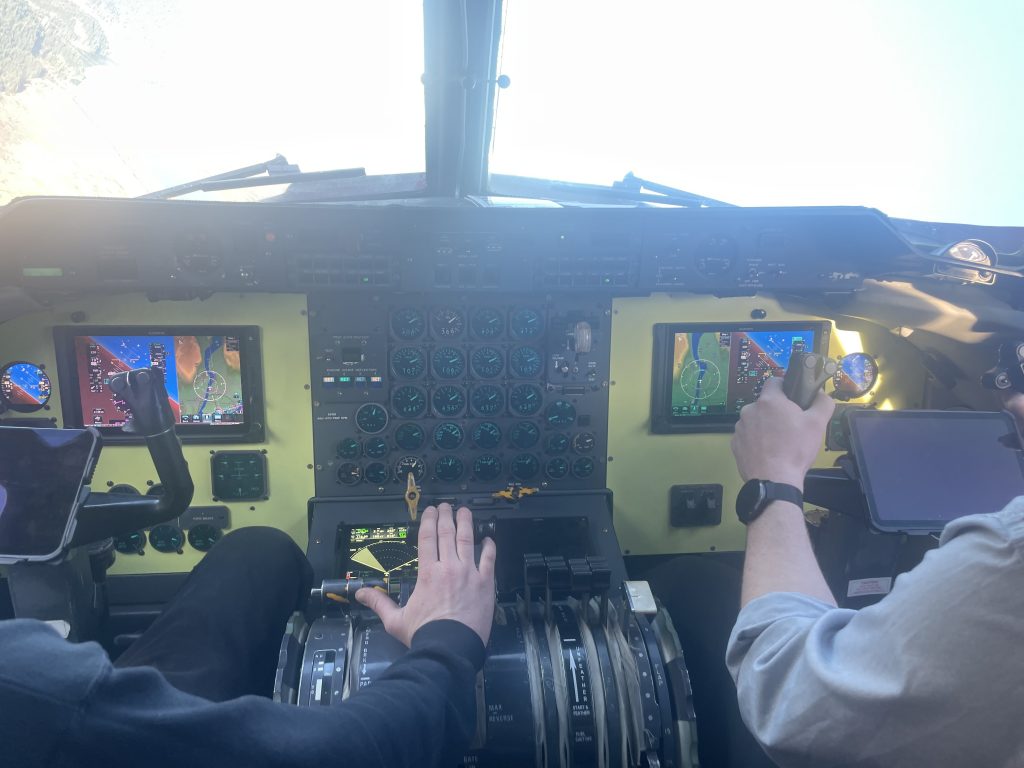
After a handful of flight tests and fixing some minor snags revealed by said test flights, representatives from Transport Canada Flight Test HQ went along to observe a full test flight, which was part of the work required to receive our Supplemental Type Certificates (STC) for this airframe. Additional Dash 7’s which will receive this modification will now undergo a more streamlined test flight program as the first aircraft proved the overall design is compatible with the airframe.
This installation and much of the design work will also translate to other airframes. With few glass panel solutions for the general aviation market, and smaller Transport Category aircraft operating in the North, we see this configuration being expanded to cover other airframes.
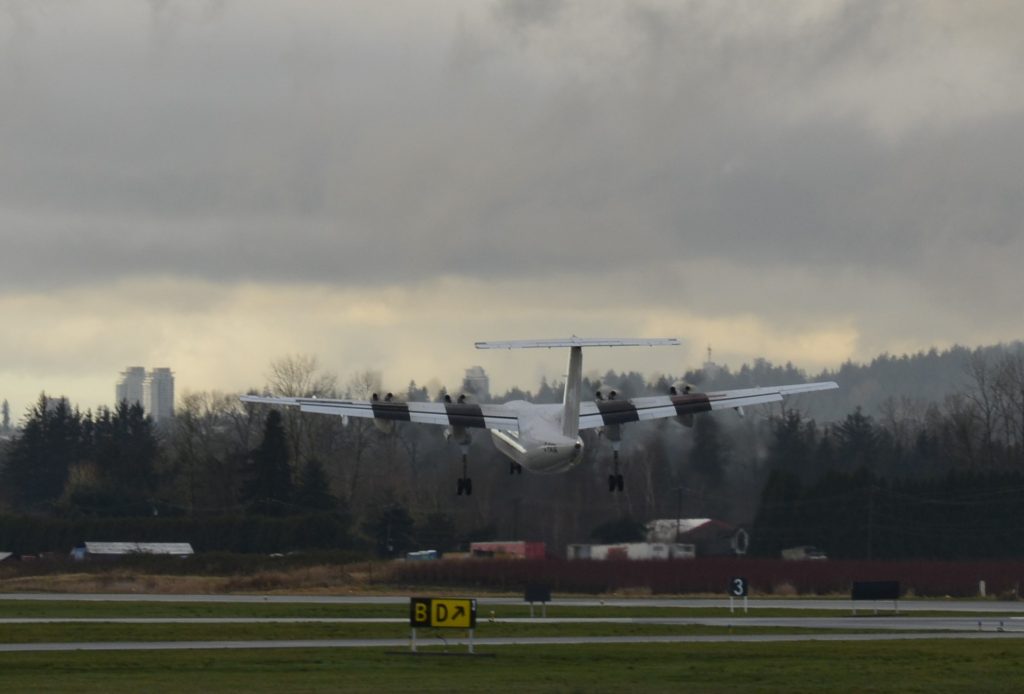
We would especially like to thank Air Tindi for their support and partnership throughout this project as we often leaned on them for their expertise on the airframe, and for flight crews during both ground and flight testing, along with their confidence that we could get this complex project across the finish line.
Chris Reynolds
President
Air Tindi Ltd.